In this article, we present several examples of reverse logistics where companies have succeeded in turning returns management into not only a competitive differentiator, but also a business model in its own right.
Return logistics is all about managing and optimizing flows from the consumer to the manufacturer. The cost of receiving, buffering, and storing returns plays the most significant role in the entire process.
Return logistics strategies
Return logistics is the process of returning a product to a retailer or manufacturer to recover its value or to dispose of it properly. It is the reverse process of the standard supply chain, i.e., the direction of getting the product to market is reversed.
Today, returns are becoming more common. According to a study by Deloitte, retailers process 13 billion returns worth nearly 2.5 trillion annually (that's four times the total value of e-commerce sales in 2018).
For this reason, companies that handle numerous returns typically employ a variety of loss mitigation strategies: repackaging products for reintroduction, recycling some materials, reusing some items (cannibalization in logistics), or, when there is no other option, simply destroying or disposing of the product to minimize its environmental impact.
In any case, the best reverse logistics strategy is the one that does not exist, because it means that the customer is satisfied with the product received and does not return it. To achieve this, it is necessary to implement a mode of operation in the warehouse that avoids shipping errors and thus increases customer satisfaction.
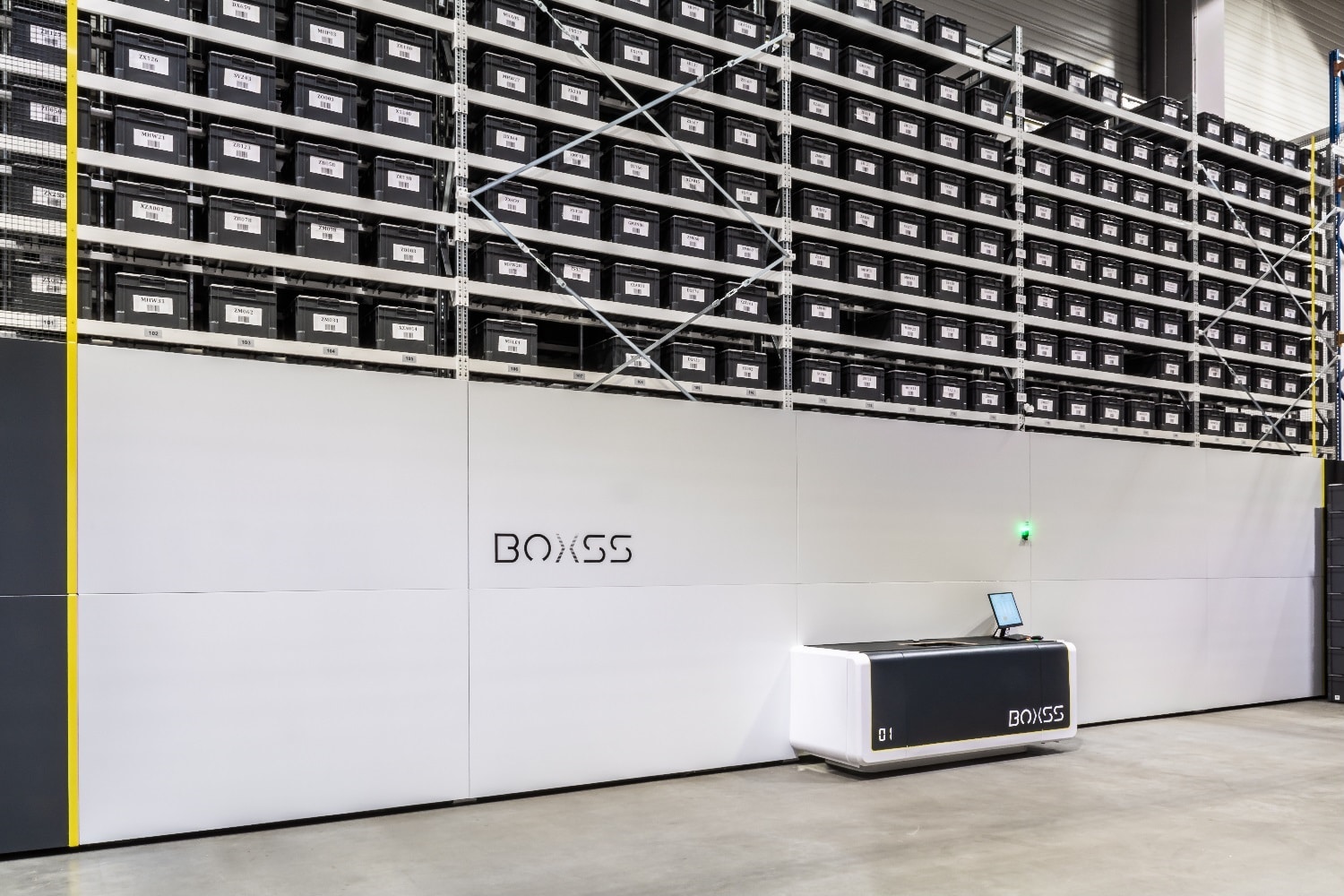
Different reverse logistics strategies
For some companies, the costs associated with reverse flows can significantly reduce their profits, sometimes to the point that the initial transaction becomes unprofitable. These companies must now understand the importance and strategic role of reverse logistics. Managers should focus on reducing these costs by streamlining aspects of reverse logistics:
- Increasing the effectiveness of security technologies,
- Accelerating disposal decisions,
- Accelerating cycle times,
- Improving data management.
The most effective way to reduce the cost of returns is simply to reduce the volume of returned products. To achieve this, a company must prevent ineligible products from entering these streams.
In addition, once the right products are in circulation, the company must move them through circulation as quickly as possible.
Reducing logistical reverse flows
New techniques have been developed to ensure that all products entering reverse logistics flows are qualified for placement in the system.
Some of these include:
- Backflow access filtering technologies,
- Product lifecycle management,
- Information systems,
- Electronic data interchange,
- Reverse logistics design,
- Product Lifecycle Management.
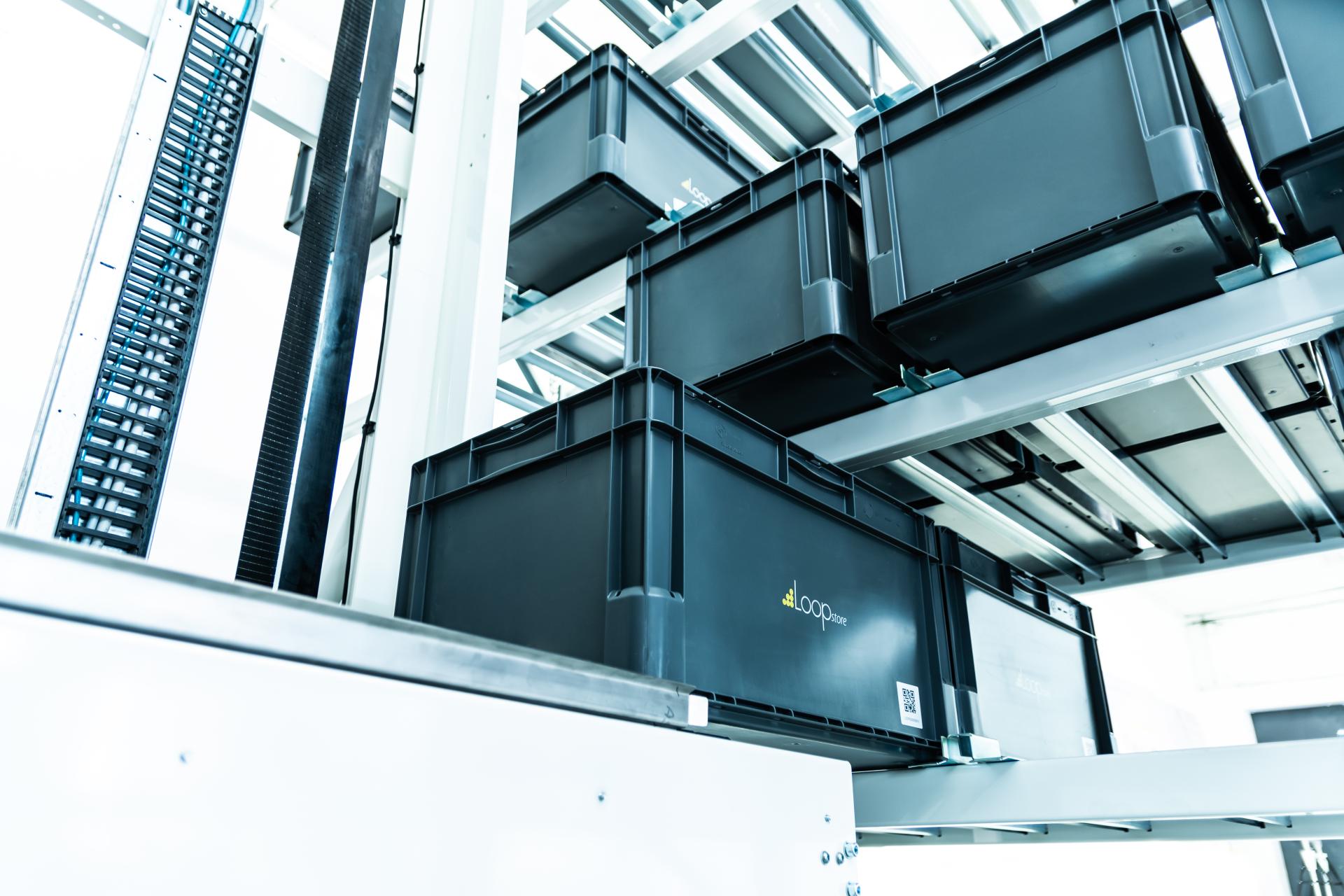
Product lifecycle management involves a company providing appropriate logistical and marketing support at various stages of the product lifecycle (launch, development, maturity, decline). Depending on the stage the product is at, the company must provide different forms of management and support. Especially towards the end of the product lifecycle, the associated inventory costs will increase dramatically. The main reasons for the sharp increase in these costs will be obsolescence and storage costs.
Companies must therefore anticipate the end of the life cycle of their products as soon as they are past the growth phase, so that fewer of them become obsolete and go into reverse circulation.
Access filtering technologies for reverse flow
Gatekeeping is the process of deciding which products should or should not be accepted into the returns' system. Improving access control will reduce the volume of returned goods, thereby reducing the overall cost of the return flow. This improvement will also require adequate employee training.
One technique currently being used to improve access filtering is to implement a web-based or intranet network that guides the employee through the return process for each product.
Electronic data exchange
Although many companies are now using electronic data interchange, they do not always find it necessary to invest in it to manage return flows. However, electronic data exchange can also be used to automate the processing of returns.
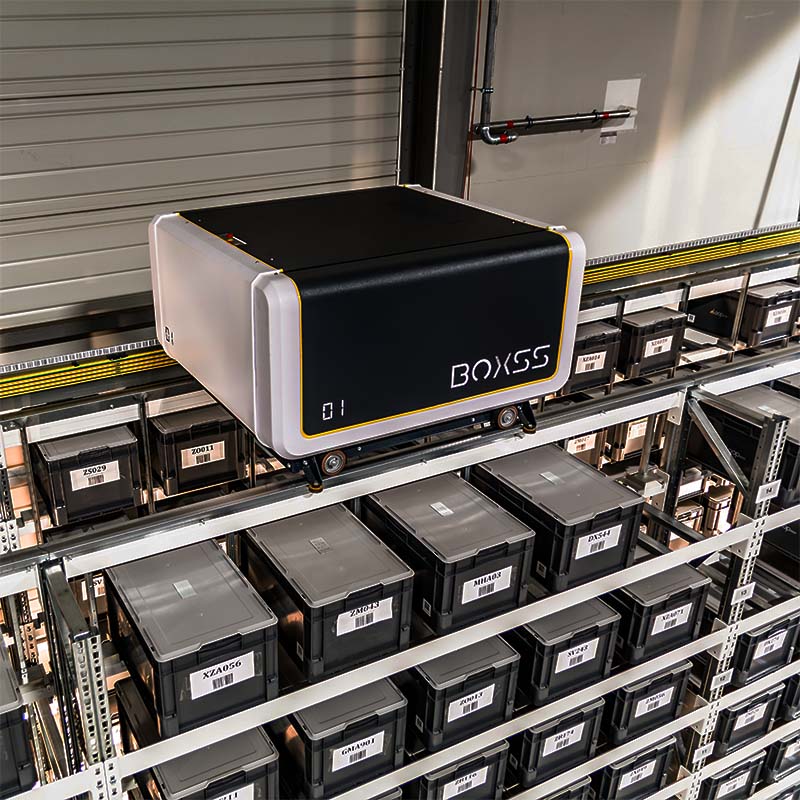
Project tailored to return logistics
Nowadays, companies often customize their products to make certain operations easier and thus cheaper. This is known as "design for manufacturing" or "design for supply chain management". Recently, this approach has begun to change somewhat.
For example, a company adjusts the packaging of a product to make it easier to return. It may also encourage the consumer to return the product in its original packaging or to return a discontinued product when they want to buy a new one.
Projecting a return logistics is thus about considering the needs of reverse logistics in the design and packaging of a product, i.e., integrating its needs and environmental protection on the one hand and the product and the reverse logistics chain on the other.
Optimizing your warehouse for reverse logistics
Assuming your business is profitable, product sales should outweigh possible returns. Certain processes are optimized to such an extent that you should not make major changes that will disrupt your previously smooth and efficient warehouse. Priority is given to fast picking and even faster shipping. Therefore, it is worth considering a side solution aimed at increasing warehouse capacity and creating a buffer zone between receipt, segregation and the final decision on whether to re-sell the product. Only at this point should the product return to the warehouse, or otherwise be disposed of.
The BOxSS system, thanks to its seamless configuration, can increase the capacity of a warehouse. If the aim is also to improve the efficiency of warehouse logistics, the solution is to add another autonomous robot. With direct access to each container, only one robot is needed to operate the warehouse without any additional equipment. In addition, BOxSS integrates with other logistics systems, so it can be part of a larger system.
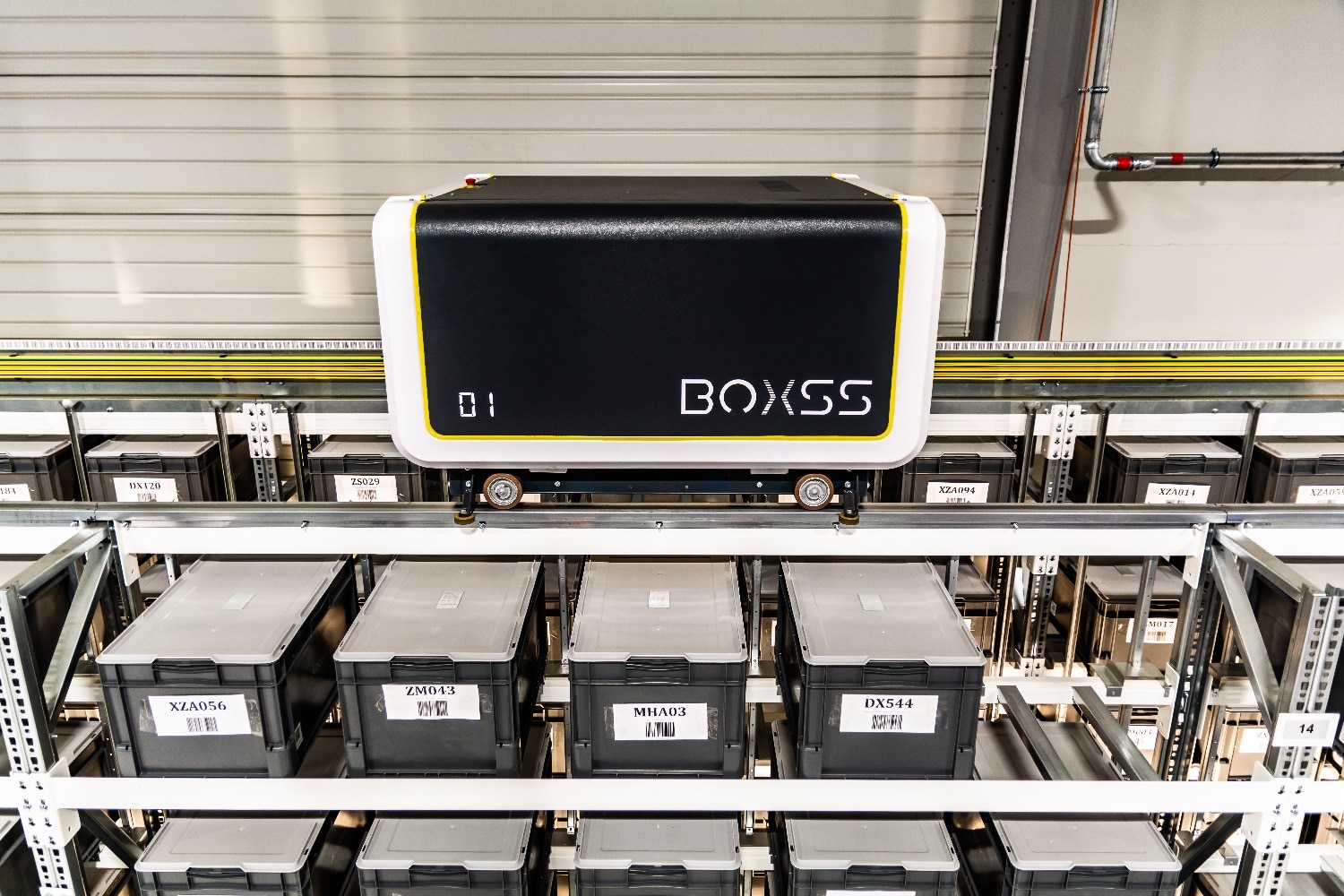
What challenges are currently facing reverse logistics?
The challenges of reverse logistics are important and should be considered in terms of brand image, sustainability and profitability.
Reverse logistics is fundamentally different from "conventional" logistics. Manufacturers and retailers design their supply chain to move a continuous flow of products from the point of production to the point of consumption quickly and efficiently.
For reverse logistics to be effective, the warehouse must be well-projected, for example by separating an area for repackaging items, and installing storage and management systems that make it easier to organize goods. LoopStore has years of experience in creating customized warehouse solutions. Contact us and we will advise and assist you in designing your warehouse.
Recent Comments