Merida to firma produkująca urządzenia i środki higieny. Przedstawiliśmy już Use Case z automatyzacji magazynu, a w dzisiejszym artykule przybliżymy następujące kwestie:
- założenia projektu,
- wyzwania, z którymi mierzyła się Merida,
- plany automatyzacji magazynu,
- propozycję projektu od LoopStore,
- plany na dalszy rozwój.
Cel projektu magazynu Merida
Przeprowadzone rozmowy z Meridą oraz analizy pomogły wyszczególnić nam główne założenia i cele projektu automatyzacji magazynu:
- ograniczenie marnotrawienia czasu na poszukiwania i uzupełniania zapasów,
- skrócenie czasu pickingu towarów,
- oszczędność miejsca i zwolnienie zajętych miejsc paletowych,
- lepsza organizacja i ergonomia pracy.
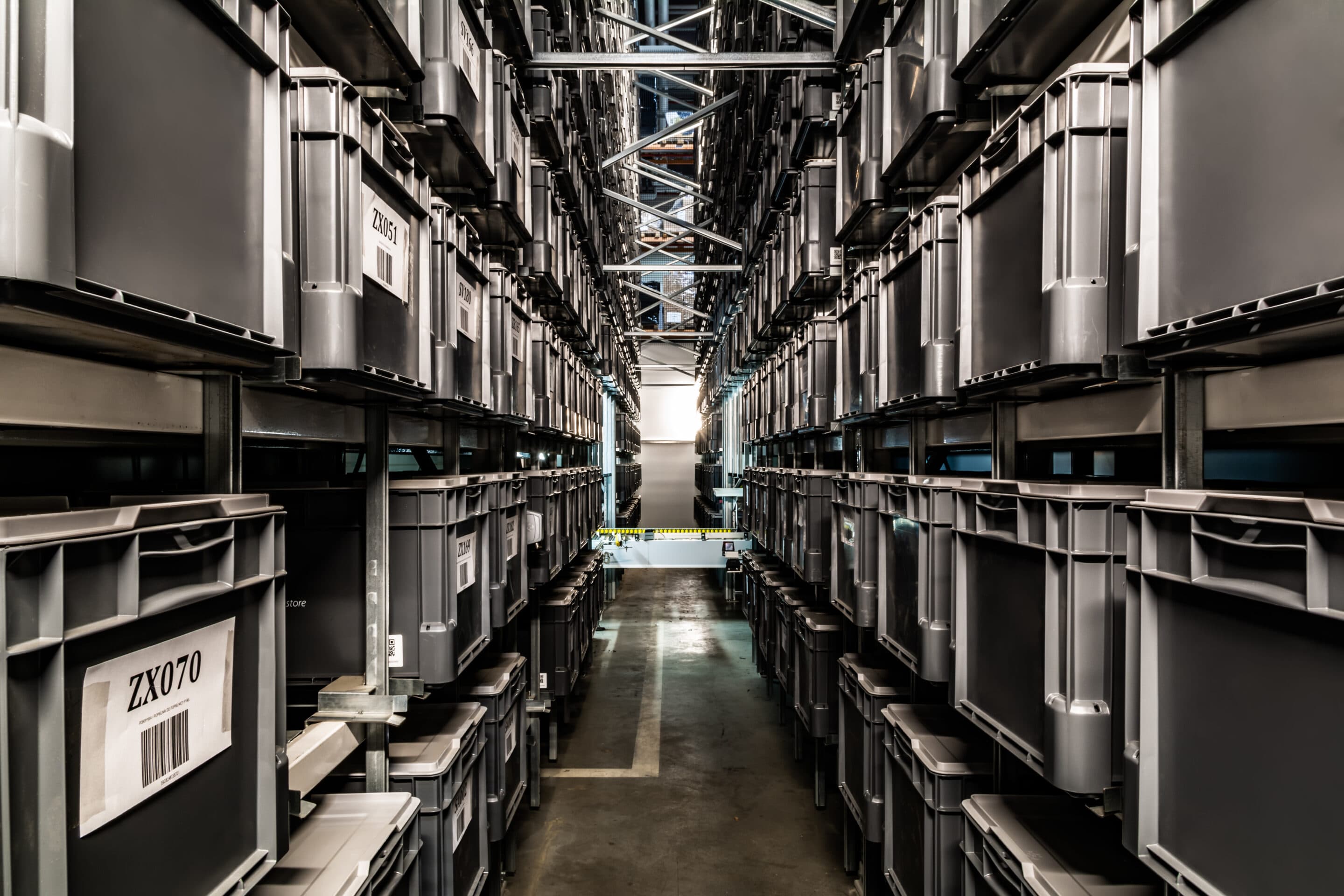
Jak było do tej pory?
Zamówienia w Meridzie podzielone są na dwie części: produkty gabarytowe oraz drobnica. Produkty gabarytowe są łatwe do kompletacji, jednak drobne produkty stwarzają najwięcej problemów i to jest obszar, który podlegał analizie.
Miejsce składowania drobnicy składało się ze ścieżki, w której po obu stornach były umieszczone regały paletowe o długości 28 m, wysokości 8 m oraz łącznej pojemności 300 palet, z czego 60 miejsc paletowych w dolnej strefie było wykorzystanych na składowanie drobnicy.
Regały były podzielone na dwie strefy. Strefa górna (znajdująca się powyżej 2 m) była miejscem składowania palet, gdzie przechowywano zapasy. Strefa dolna (poniżej 2 m) była miejscem na kuwety i pojemniki, w których rozlokowywano produkty. Kolejnym etapem było pobieranie dzięki pickerowi według złożonego zamówienia.
Co jakiś czas produkty w dolnej strefie były uzupełnianie. Polegało to na zdjęciu z góry palety z zapasami, odszukaniu brakujących elementów i ich uzupełnienie. Czasami zdarzało się tak, że braki w dolnej strefie nie były uzupełniane na czas, co powodowało przestoje podczas kompletacji i przeorganizowanie pracy z powodu konieczności ściągnięcia z góry palety i odszukania potrzebnych elementów.
Picker, nie był wyposażony w odpowiednie narzędzia do ściągania palet i uzupełniania zapasów, przez co każdorazowo konieczny był udział dodatkowej osoby z wózkiem widłowym oraz dostępem do systemu, żeby po uzupełnieniu zapasu odnotować ten fakt w WMS/ERP.
Jakie były plany na optymalizację procesu magazynowania i kompletacji?
Merida, żeby zwiększyć efektywność pracy oraz zoptymalizować miejsce składowania, chciała zastosować antresolę 4 poziomową z regałami półkowymi, na których miały być przechowywane wszystkie drobne towary, zarówno te do bieżących operacji jak i zapasy, które wcześniej były składowane na paletach.
Zastosowanie antresoli magazynowej to standardowe rozwiązanie w takich sytuacjach, ale stwarza pewne niedogodności.
- Operator musi chodzić po trzech poziomach antresoli, przez co zaoszczędzony czas na uporządkowanym składowaniu jest tracony na przemieszczanie się.
- Antresola jest miejscem pracy i musi spełniać wszystkie wymogi ergonomii, bezpieczeństwa i BHP, a to wiąże się z zachowaniem odpowiednich prześwitów na każdym poziomie, odpowiednim oświetleniem, system p.poż. na każdym piętrze, klatką schodową, korytarzami komunikacyjnymi i ewakuacyjnymi.
- Wielkość planowanej antresoli to 110 m2/poziom, co w całości daje 440 m2, z czego tylko 40 m2/poziom zajętej powierzchni to regały, a reszta to przejścia komunikacyjne, miejsca zasilania towaru oraz klatka schodowa. Efektywne miejsce składowania dla całej antresoli to zaledwie 160 m2, czyli ok. 36% całej zabudowy.

Propozycja automatyzacji magazynu od LoopStore
Mając na uwadze wszystkie potrzeby i wymagania Meridy, zaproponowaliśmy instalację magazynu automatycznego o wysokości 7 m i długości 15 m. Jego łączna pojemność to 650 pojemników o wymiarach 600x400x320 i maksymalnym obciążeniu 25 kg. Aby efektywnie wykorzystać pojemność, każdy z pojemników może zostać podzielony na 6 części, co pozwala na przechowywanie do 6 różnych produktów – SKU na pojemnik. Takie rozwiązanie eliminuje zajmowanie lokalizacji z niezapełnionymi pojemnikami.
Zasada działania systemu BOxSS polega na dostarczaniu towaru do człowieka (do stacji GTM). Z jednego miejsca (przy stacji GTM) odbywa się pobieranie (picking) oraz zasilanie magazynu. Czas dostarczenie pojemnika do stacji to co najwyżej 60 s.
System pozwala na konsolidację zamówień, dzięki czemu kompletacje zostały jeszcze bardziej zoptymalizowane, a całość systemu bardziej wydajna. Projekt został wyposażony w pojemniki z pokrywkami. To rozwiązanie pozwoliło na zmniejszenie instalacji tryskaczowej o 70%, co bezpośrednio przełożyło się na zwrot z inwestycji – ROI.
Korzyści z zastosowania systemu BOxSS
- Dzięki zastosowaniu BOxSSa wyeliminowana została konieczność chodzenia operatorów, ponieważ wszystko odbywa się w jednym miejscu.
- Uniknęliśmy strat czasu związanych z niedoborami elementów podczas kompletacji.
- Zwolniło się 60 miejsc paletowych.
- Projekt umożliwił zapanowanie nad stanami magazynowymi, a także znacznie wyeliminował błędy kompletacji.
- System w połączeniu z programem WMS/ERP wyeliminował kartki kompletacyjne i związane z tym błędy.
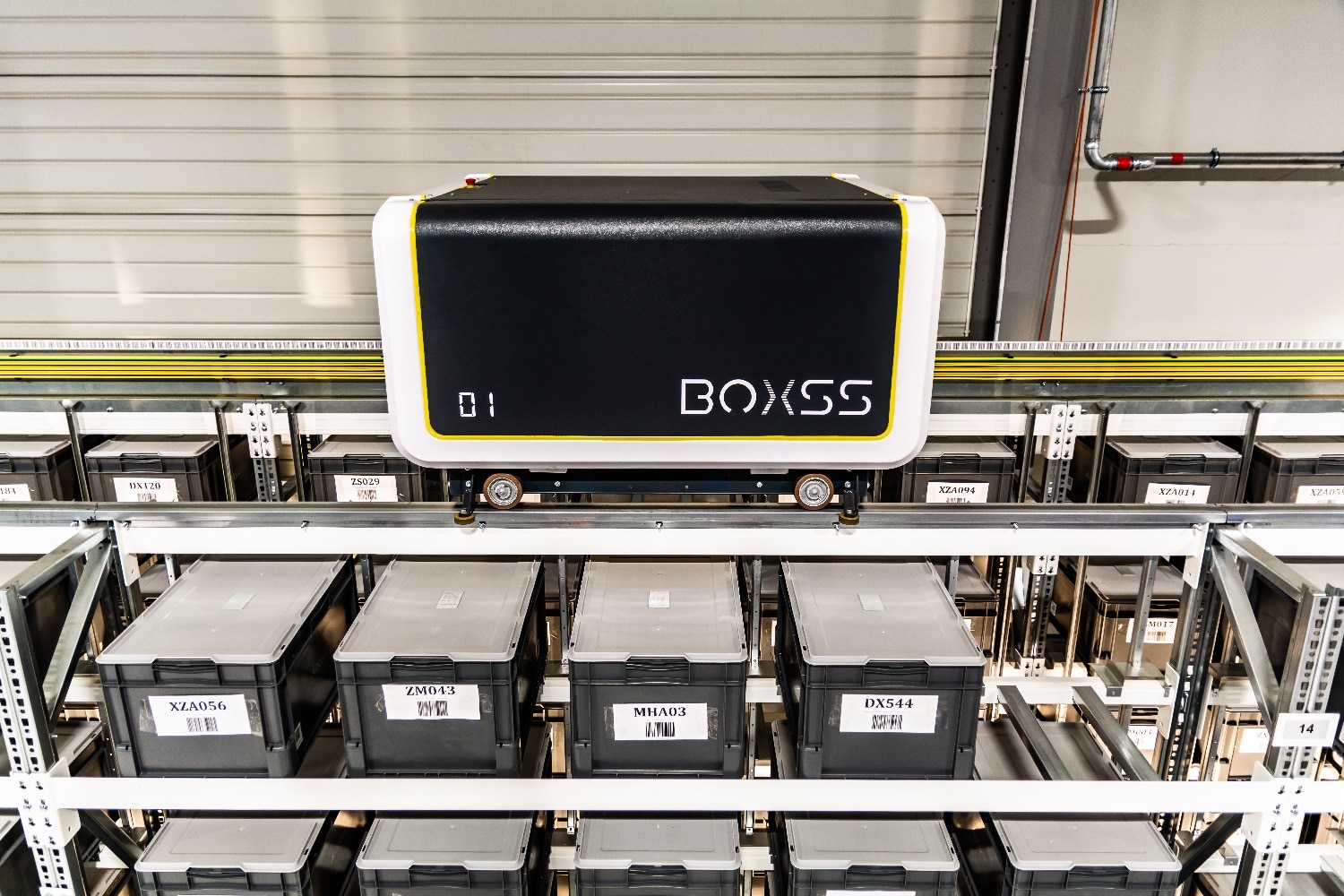
Wprowadzenie nowych towarów nie wymusza na operatorach konieczności „zapamiętania” kolejnych lokalizacji z produktami. Po pół roku działania systemu BOxSS, pojawiła się jeszcze jedna nieoczekiwana przez klienta korzyść. Występująca częsta rotacja pracowników nie sprawia dużego problemu, ponieważ nie ma konieczności nauki pickerów miejsc lokalizacji towarów. To znacznie skraca proces szkolenia i pozwala szybciej osiągnąć pełną efektywność nowego operatora.
System BOxSS w magazynie Meridy zajmuje zaledwie 30 m2, posiada osłony zamontowane bezpośrednio na konstrukcji, co nie zajmuje dodatkowej przestrzeni magazynowej i pozwala na dodatkowe składowanie w bezpośrednim sąsiedztwie magazynu.
Możliwość dalszego rozwoju
BOxSS w prosty sposób można rozbudować o kolejne moduły, dzięki czemu bez dużych nakładów finansowych można powiększyć pojemność oraz wydajność magazynu. System wdrożony w Meridzie został przygotowany tak, żeby można było powiększać go o kolejne moduły.
Najnowsze komentarze